Overall Equipment Effectiveness (OEE) is a metric used to measure the effectiveness and performance of manufacturing processes or any individual piece of equipment. It is a combination of metrics that addresses how effectively a manufacturing operation is utilized. By monitoring OEE, manufacturers can quantify and measure equipment potential and identify sources of loss. OEE is widely recognized as a key performance indicator (KPI) for manufacturers in various industries.
Benefits of OEE
Some of the benefits of measuring OEE include analyzing production, reducing costs, improving quality, increasing capacity, and/or increasing efficiencies in production lines . Measuring OEE can also help manufacturers identify the underlying issues and root causes of machine downtime, slow cycles, and defects . By having a predetermined framework of the impact of machine availability, performance, and quality, OEE provides a framework to track underlying issues and root causes which can then be resolved. through improvements in the manufacturing process.
Calculation
OEE is calculated by multiplying three factors: Availability, Performance, and Quality. Availability measures the percentage of time that the equipment is available for production. Performance measures the speed at which the equipment is running compared to its maximum speed and lastly, quality measures the percentage of good parts produced compared to the total number of parts produced.
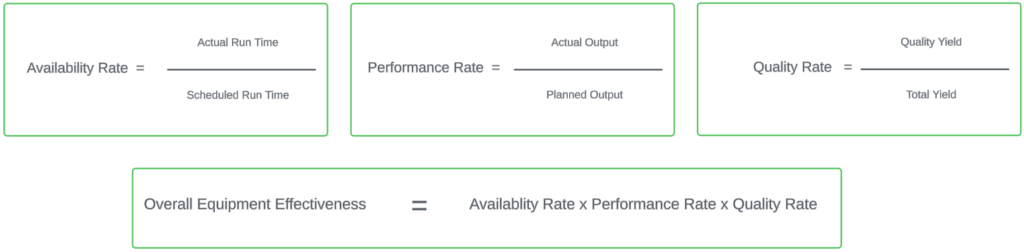
When calculating Availability, it is often easier to measure the time periods where the machine is not operational when it should have been. Another way to think about this is downtime, whether due to downtime or when the machine has not been configured for its intended use. Using that time period, express it as a percentage and take it away from 1 i.e., 1 – downtime %. As an example, if we take a common operating work shift of 8 hours but for 1 hour the machine was not operable when it should have been, then the Availability measure will be 87.5% i.e., (7 operable hours/8 total hours).
For measuring Performance, it is best to think of it as measuring how much the machine creates as output compared to its theoretical or desired quantity. If a machine is capable of producing 5000 units of an output during a particular operational period but only produces 4,000 units, then the Performance measure is 80%, calculated as 4,000/5,000.
Lastly, the Quality measure looks at the total output of the machine and determines how many met the required standards as set by the customer or process. Taking the 4,000 number above from the Performance measure that was produced, and determining that only 3,600 of those met the standard, the Quality measure is then 90%.
From there, we multiply the three percentage values from above, 87.5% x 80% x 90% = 63%. The resulting figure is your Overall Equipment Effectiveness.
The goal is to get the resulting OEE figure as close to 100% as possible. Understandably it is impossible to always achieve 100%. Things break down or don’t go as planned.
What Can Be Done With OEE?
A Note On Quality
Traditionally, the OEE would tell us where we are experiencing issues whether that is the Availability, Performance or Quality and at first glance, it would be easy to focus on the metric that yielded the lowest result.
However, from my experience, Quality should be the priority in OEE when it comes to prioritizing improvement initiatives. If the percentage of quality output compared to the total is low, it does not make much sense to try to improve the machine availability or its performance – improving those two metrics will only serve to produce more low-quality output which means more waste, rework and/or scrap.
Before starting improvement work to the availability or performance, the quality output should be as high as possible. In the world of Six Sigma, this should be 99.9997%. Of course this will depend on your industry.
The 6 Big Losses
The attainment of optimal OEE can be significantly impacted by what’s commonly referred to as the “6 big losses.” These losses include various inefficiencies or wastes that erode equipment effectiveness and overall productivity.
- Equipment breakdowns: Downtime caused by unexpected failures or breakdowns in machinery.
- Setup and adjustment time: Time required for equipment changeovers or adjustments between different products or processes.
- Idling or minor stoppages: Short pauses or interruptions in production that collectively impact continuous operation.
- Reduced speed: Operating below the maximum potential speed or capacity of the equipment.
- Process defects: Production of faulty or substandard goods that don’t meet quality standards.
- Start-up rejects: Initial batches of production that are discarded due to quality issues or failures during the start-up phase.
The first three losses—downtime due to equipment breakdowns, setup and adjustment time, and idling or minor stoppages—directly impact the availability factor of OEE.
These three losses can be mitigated through the use of Lean tools including Total Productive Maintenance which will reduce the occurrence and impact of machine breakdowns and SMED (Single Minute Exchange of Die) which can reduce time lost due to changeovers.
The other three losses—reduced speed, process defects, and start-up rejects—adversely affect the performance and quality aspects of OEE. Reduced speed implies the equipment operates slower than its potential maximum speed, process defects lead to the production of faulty or substandard goods, and start-up rejects involve initial batches being discarded due to quality issues, all leading to diminished performance and quality metrics within the OEE framework.
Mitigating these six significant losses is crucial to enhancing OEE and maximizing overall equipment effectiveness in manufacturing environments. By identifying these sources of waste, the organisation can create initiatives to reduce, or wherever possible, entirely remove these sources of waste.
Implementing Overall Equipment Effectiveness
Implementing Overall Equipment Effectiveness (OEE) involves a systematic approach to measure the productivity of manufacturing equipment. Here’s a comprehensive step-by-step guide to implement OEE effectively:
Step 1: Understand OEE
Conceptual Understanding: Familiarize yourself and your team with the concept of OEE. It measures the efficiency of manufacturing processes by combining availability, performance, and quality metrics.
Everybody in your operation should have an understanding of what the OEE is and how it is calculated. Even if they aren’t involved in the calculating itself, they should understand the principles behind it. This is a key part of Change Management where people are informed and involved.
Step 2: Select Equipment and Processes
Identify Equipment: Choose the specific machinery, equipment, or processes you want to measure with OEE. Start with a pilot project or a limited number of machines for initial implementation.
Ideally the machine you pick should be the one that may be a bottleneck or constraint within your processes. As per the Theory Of Constraints, the output of your entire organisation (i.e., system) is limited by the constraint. If the constraint is a machine, then any improvements via removing waste on the machine will directly improve the output of the organisation.
Step 3: Gather Data
Collect Data: Create log sheets that detail issues that you come across. This includes downtime periods, number and duration of minor stops, changeovers, amount of output and quality of that output.
Step 4: Analyze and Calculate OEE
Calculate OEE: Use the formula and detailed description above for how to calculate and understand the results of the OEE.
Step 5: Identify Improvement Opportunities
Analyze OEE Data: Review OEE scores to identify areas for improvement. Focus on the components—availability, performance, and quality—that contribute to lower scores but as stated above, quality should be given priority.
Tip: Look for other tools available within Lean and Six Sigma to implement. Examples include Total Productive Maintenance, SMED, Quality Controls and Assurance, Data Analysis etc.
Step 6: Implement Improvements
Develop Action Plans: Create strategies to address identified issues. This could involve maintenance schedules, process optimization, training, or quality control measures.
Always make sure to communicate these changes to staff before implementing them with detailed explanations of what issues these improvements are expected to address and the impacts it will have on them.
Step 7: Monitor Progress
Track Changes: Continuously monitor OEE scores after implementing improvements. Evaluate the impact of changes made and make adjustments as necessary.
Step 8: Document Processes and Implement Controls
Document Processes: In order for processes to not regress back to the way it used to be, the new process should be documented and made available to every employee involved. These documents will also act to educate new staff and over time, the ways of working can be checked against these documents.
Implement Controls: Just as with documenting the process, controls need to be implemented so that processes don’t regress back. Controls can be as simple as reminders in written form located at strategic locations in the operation where they are easily viewable by staff to act as reminders.
Additional Tips:
- Training and Education: Ensure that the team involved understands the significance of OEE and how it relates to their work.
- Benchmarking: Compare your OEE scores against industry standards or similar operations to gauge performance and set realistic improvement targets.
- Team Collaboration: Foster collaboration among maintenance, production, quality, and management teams to address OEE issues collectively.
Alternate Calculation
An alternate method to calculate OEE is as the ratio of Fully Productive Time to Planned Production Time. Fully Productive Time is just another way of saying manufacturing only Good Parts as fast as possible (Ideal Cycle Time) with no Stop Time. The simple calculation of OEE is: OEE = (Good Count × Ideal Cycle Time) / Planned Production Time.
While this alternate calculation is simpler, it is not as helpful in detecting issues within the manufacturing process. The key use of this method is after improvements have already been made to the availability, performance and quality of the output, and therefore, this calculation can be used simply as a maintenance measure. If it stays high, there is less to worry about but any time it breaks below a threshold, that is when management can then use the primary calculation to identify the root cause and action a solution.
Conclusion
Measuring OEE can help manufacturers identify areas for improvement in their production processes, reduce downtime and waste, increase productivity, and improve profitability. By focusing on potential and the sources of loss that prohibit equipment potential from being reached, OEE has become the de facto approach to identify improvement opportunities. It can also extend the useful life of equipment through increased awareness and focus on machine health and productivity.